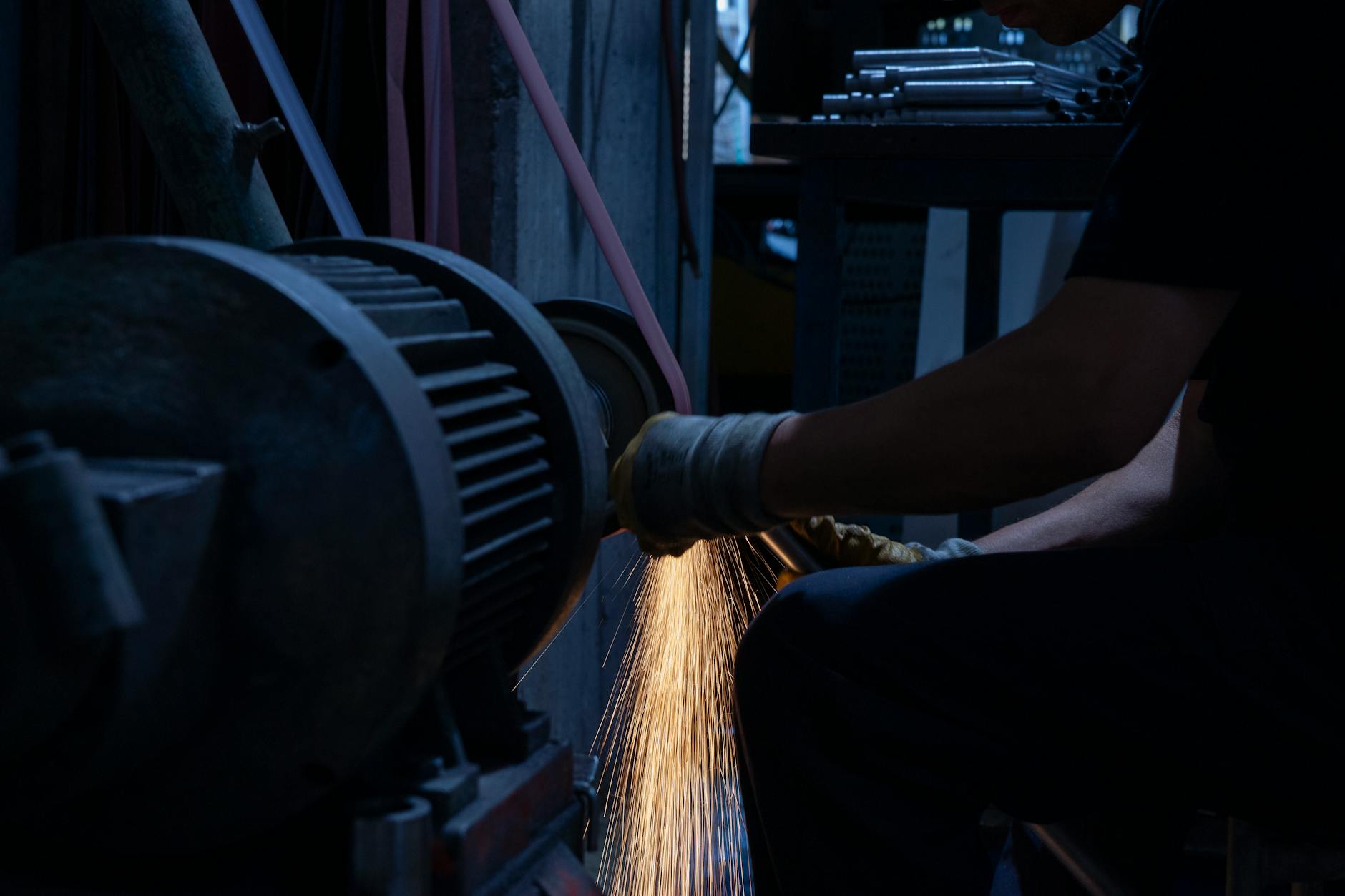
OUR SERVICES
We take care of everything, from design to finishing
360° Solutions, from Design to Realization
At DMP, we offer a complete service for every need in steel and special alloys processing, supporting the client throughout all stages of the production process.
Whether it is a single component or a complex project, we guarantee precision, quality, and reliability, combined with the flexibility of a structured company and the support of experienced technicians.
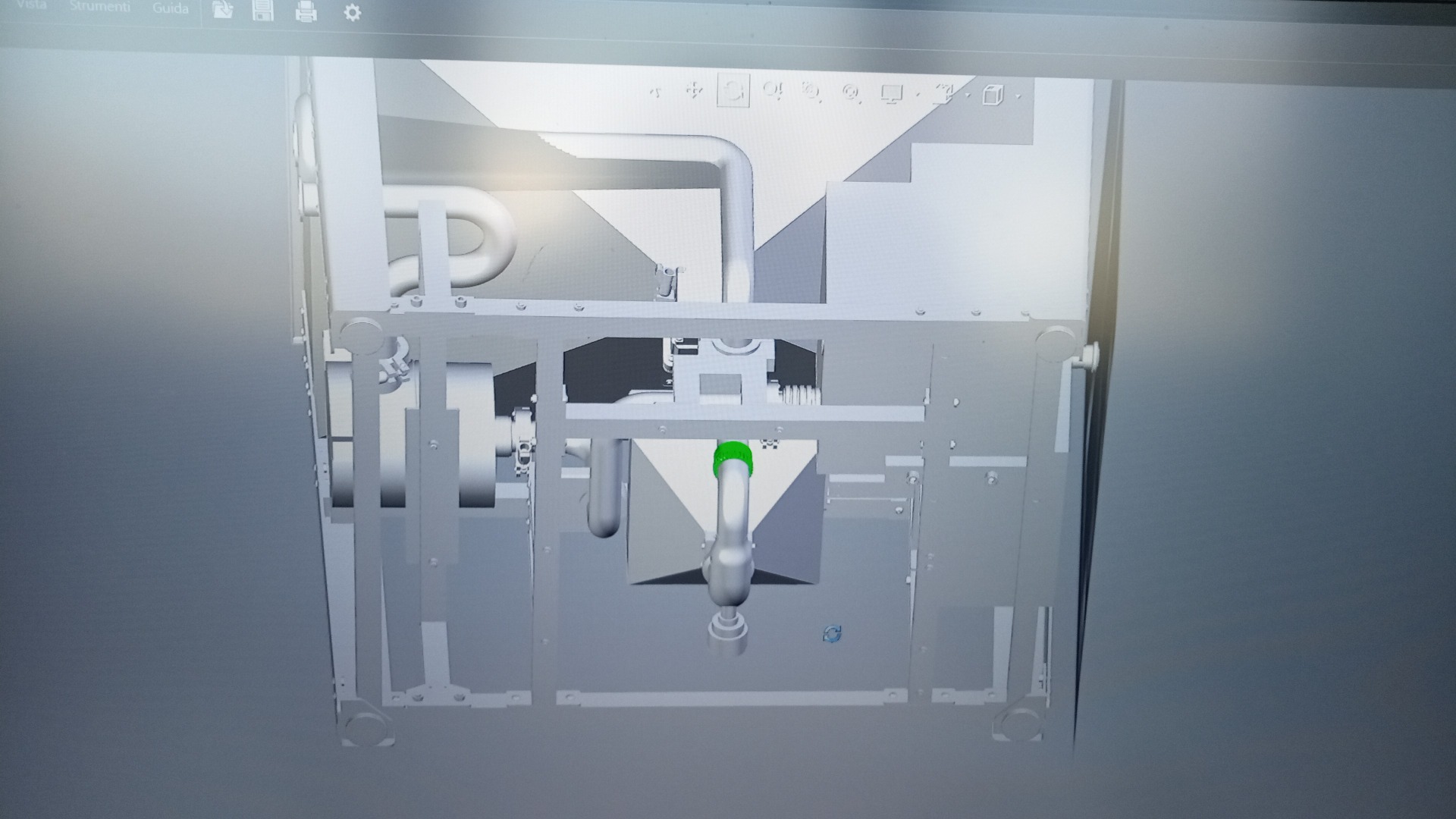
DESIGN AND TECHNICAL SUPPORT
Every machining process begins with a thorough technical analysis. At DMP, we offer our experience to assist the client in design or to optimize existing drawings. We evaluate the geometry of the parts, sheet metal development, critical dimensions, thicknesses, and welding details, with the goal of simplifying the production process and reducing the margin of error.
The preparation for cutting and bending is done internally, as well as the bills of materials and all the documentation necessary for traceability and quality control.
We don't just "execute" — we provide concrete technical input during the preparation phase, because we know how much of a difference it can make to the final result.
CUTTING OF TUBULARS, PROFILES, OR SHEETS
We perform material cutting using reliable and versatile equipment suited for different types of products and thicknesses. We use an FB Jupiter automatic bandsaw, ideal for precise and repeatable cutting of tubulars, flat bars, and metal profiles. Thanks to automatic programming and controlled clamping, we can achieve uniform cuts even on series production pieces, reducing margins of error and ensuring a high-quality finish on the edges.
For sheet metal, we use an industrial shear, which allows fast and clean cuts without overheating the material or altering its mechanical properties. This type of cutting is particularly suitable for thin to medium thicknesses, where speed and dimensional precision are required.
The entire process is managed with close attention to tolerance, perpendicularity, and preparation for subsequent operations, to guarantee geometric consistency on every piece.
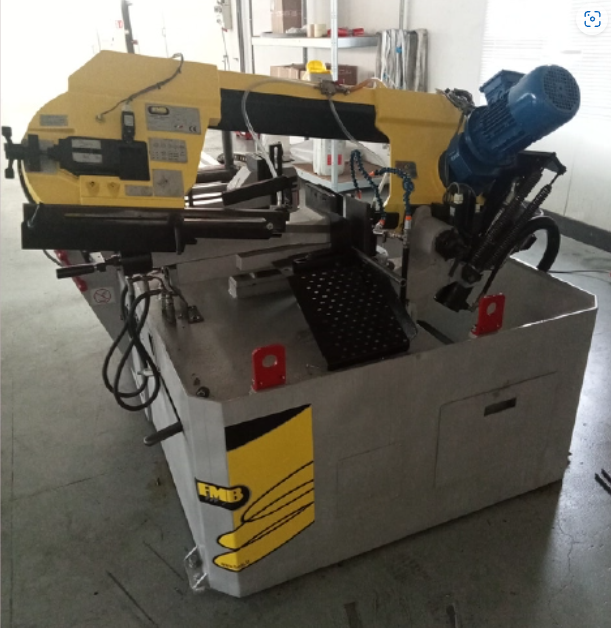
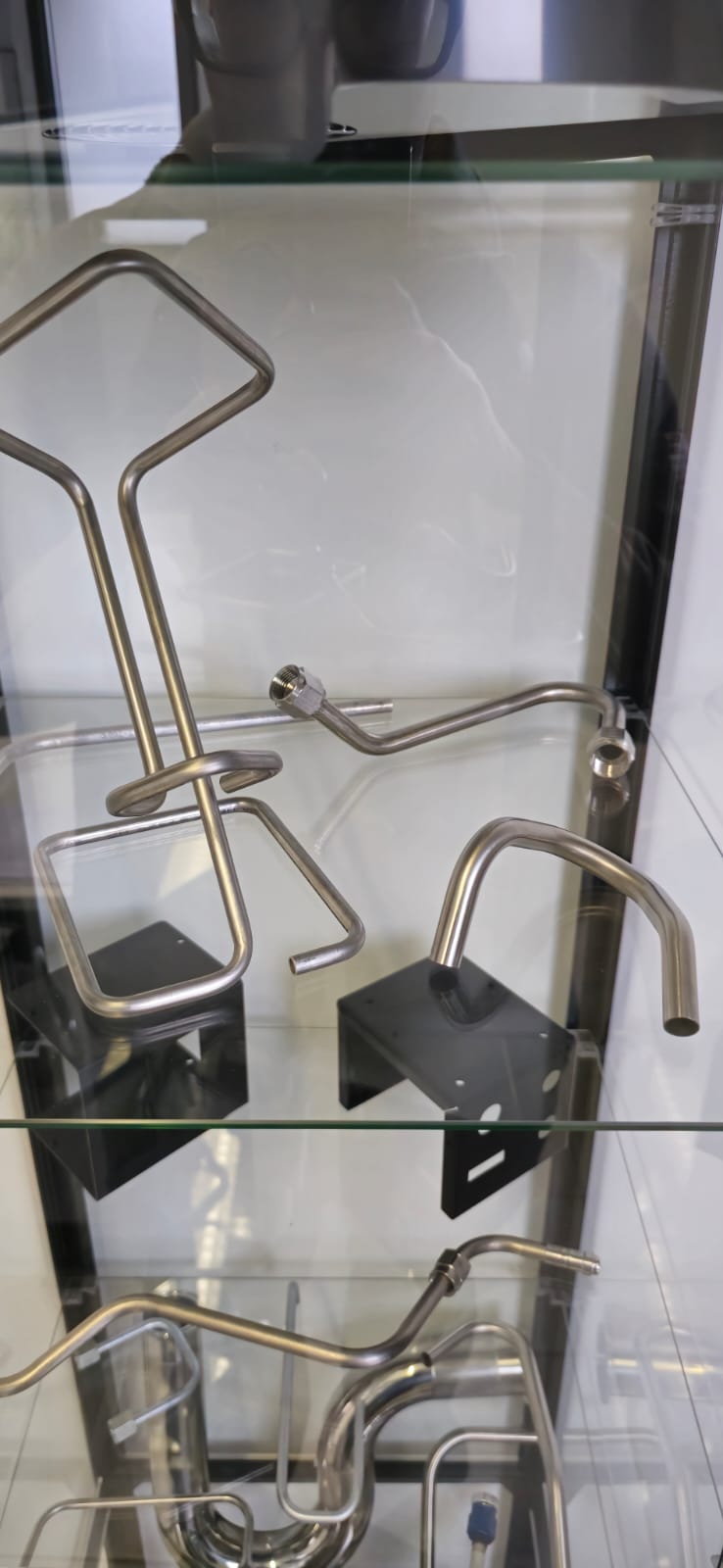
CNC BENDING
For sheet metal bending, we use a Schiavo CNC press brake, a reliable machine that allows us to work with precision on lengths up to 3 meters. Parameter settings are controlled numerically based on thickness, material type, and required angle. This enables us to achieve clean, uniform, and repeatable bends, suitable both for single pieces and larger production runs.
For tube processing, we use a Crippa 42 CNC tube bender, which allows the creation of complex and precise curves while maintaining control over the bending radius and profile deformation.
Using these two machines, we can internally and directly manage both the bending of flat components and the curvature of tubular elements, ensuring continuity between different processing phases and reliability in the final result.
WELDING
We perform welding on steels and metal alloys using MIG/MAG, TIG, and electrode methods, depending on the type of material, thickness, and geometry of the piece. Each technique is applied thoughtfully, considering accessibility, required aesthetics, and the mechanical characteristics of the joint.
The continuous wire process (MIG/MAG) is used for medium to thick sections, ensuring good speed and strong penetration. TIG welding is reserved for finer details, visible work, or thin sections where greater precision and finish are required. The electrode method is used in specific situations, such as welding on structures exposed to particular conditions or in less accessible areas.
Our focus is always on the regularity of the weld bead, the cleanliness of the heat-affected zone, and geometric consistency, to ensure reliable, continuous, and visually clean results.
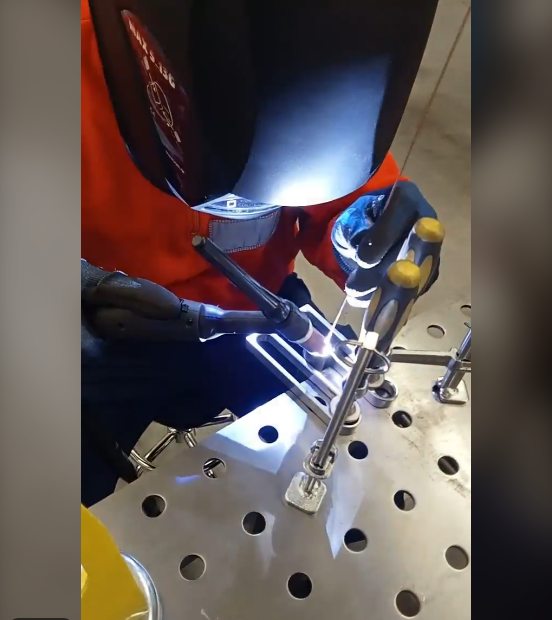
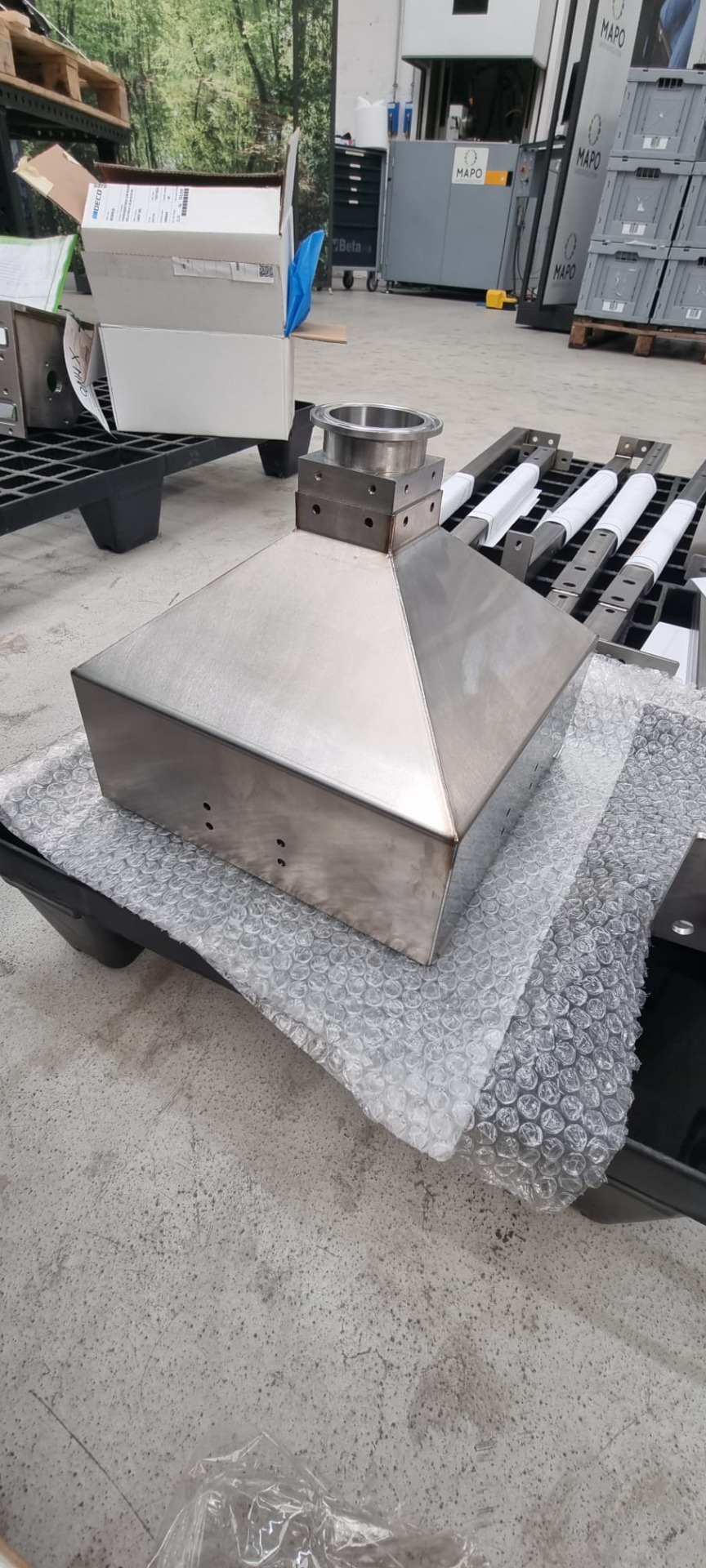
ASSEMBLY
In addition to producing individual parts, we handle the complete assembly of groups and subassemblies. This means mechanically fitting or welding multiple components together, installing threaded inserts, bushings, studs, or other accessories, and creating ready-to-use assembly kits.
The assembly is performed on equipped workbenches, with careful control of fitting tolerances and dimensional checks.
For us, it is important that everything leaving our workshop is ready to be installed or used, without the need to go back for modifications or adjustments.
PAINTING AND FINISHING
The finishing phase is often what determines the perceived quality of a product. For this reason, we carefully prepare surfaces through sandblasting, grinding, or satin finishing, depending on the type of material and its final use.
We manage industrial painting cycles internally, both liquid and powder coatings, including zinc-based primers for corrosion protection. Upon request, we can provide specific surface treatments such as hot-dip galvanizing, passivation, pickling, or shot peening through qualified partners.
Every treatment is documented and verified to ensure that the piece meets both aesthetic and functional specifications.
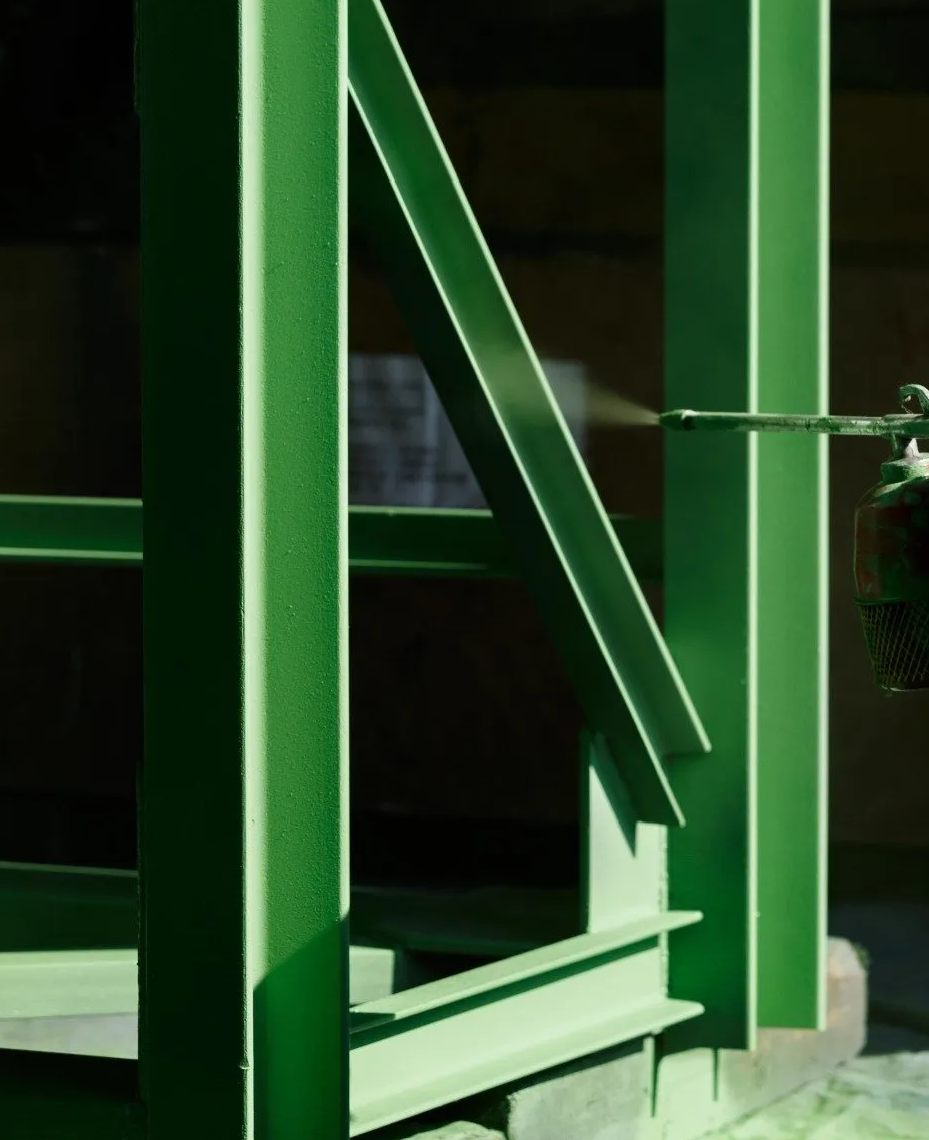